A few months ago, a long term client asked me to restore two antique side-tables for him. These two tables were originally made for his father in the Congo sometime in 1930.

The tables had suffered from moving to three different continents, and the results of changes in humidity and some dodgy repairs attempts. The top of one was seriously warped and needed a lot of careful work with a hand plane. It was made of one solid piece of rosewood, and I couldn’t risk running it through a thickness planer for fear it would break in half.

This was followed by working both sides over with a card scraper.
Perhaps the most difficult part was fitting the feet of the legs with thick sheets of copper, drilled and screwed into place. The difficulty was because everything about these tables was hand made with no two pieces exactly the same. On top of that, the legs were badly warped and twisted. So each sheet of copper had to be individually fitted into the feet. This meant that I had to clamp the legs together, make individual cardboard templates for each foot, cut these out of the copper sheets, and then inset them into the feet. One I had the copper feet properly fitted, I clamped them into the legs and marked them for drilling. Many hours were spent at my drill press first drilling the correct holes and then drilling matching pilot holes for the screws in the legs.

At this point, no carving was done, but don’t worry, that’s still coming.
Next, the owner asked me to make the two tables match a little better. One table had nice arabesque cutouts in the legs. The other table had solid legs. So I made a template for the cutout, bought a new blade for my bandsaw and with a lump in my throat, I started cutting into the solid rosewood legs.


After a quick clean up to remove the saw marks, it was time to restore the carved elements. I pulled out my chip carving knife and went at the repetitive work of skim-cutting surfaces of the diamond facets on the legs. On the legs that I cut the arabesque shapes out, I used a scratch stock to etch a line around the shape, matching the other table legs. 


Once this was done, I took the card scraper to the legs, touching the tops and legs with 400 grit sandpaper afterwards to soften the edges a little.
now to what type of finish to use! The client really didn’t want the carved diamonds to fill with lacquer or varnish thereby muting the crisp cuts. So I chose Tung Oil which would soak in and form a very thin layer, yet still have the soft sheen of the rest of the woodwork in his estate home. This was a labour intensive choice as it turns out. I ended up putting on 6 coats, which were hand rubbed with cotton cloths, and then, 24 hours later were buffed by hand before the next coat of oil was applied. After a week of drying and curing it was time to put the tables together.



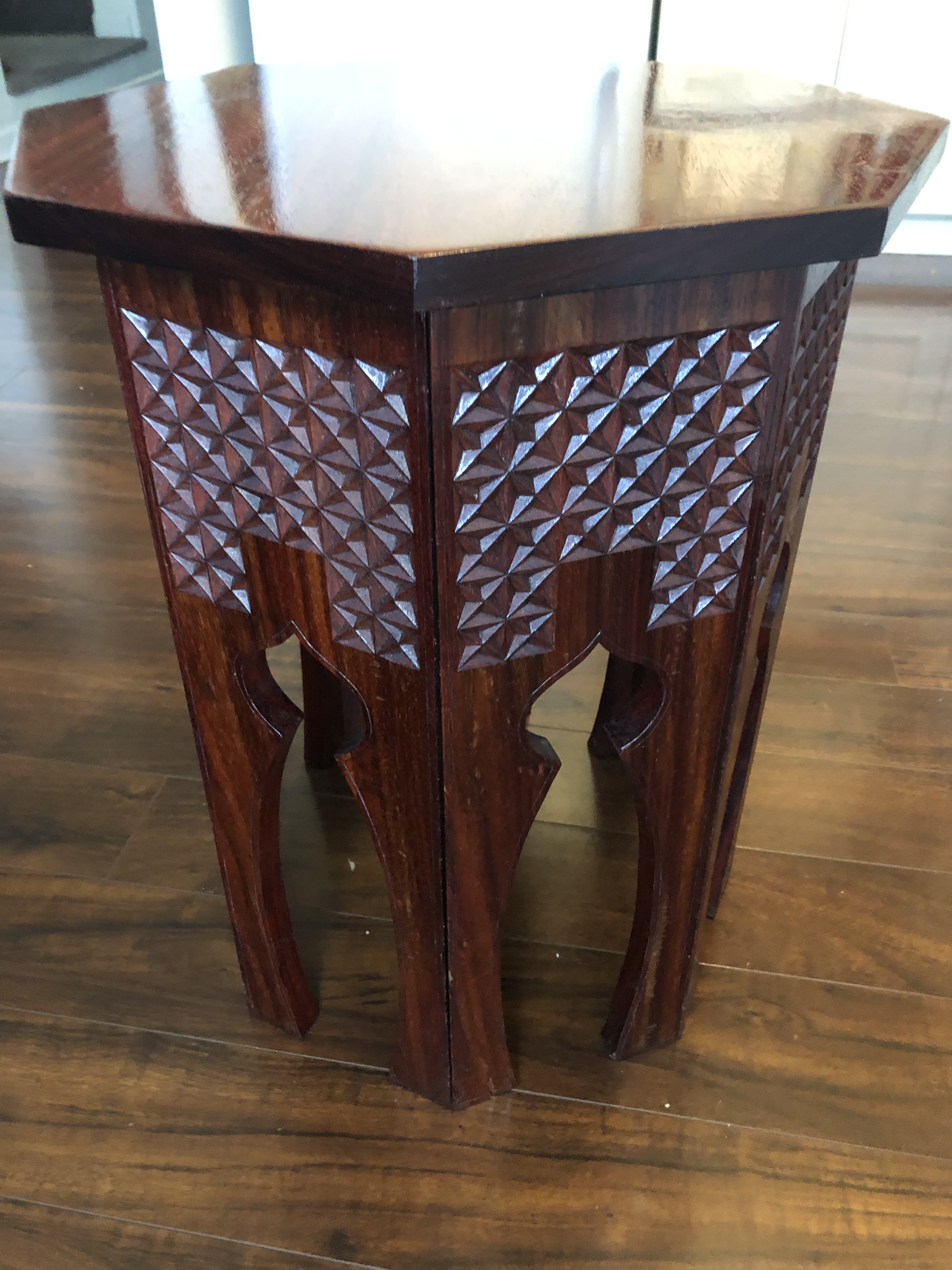
The delivery of both tables ended with a surprise. The client has a book stand from the same place and era that he wanted restored in a similar fashion. I went home with another job!


Woodcarvers need to be creative and in some cases, we need to have technical woodworking skills too. I am thankful for men like my father and his good friend Ivor Monahan, and my shop teachers years ago for the good training and showing me that every problem has a solution. This project had more than its share of problems, but with time and resources, I was able to make it work out!
Mostly I am thankful for a client who trusts me with his antique heirlooms.
Grant McMillan